Recognizing Porosity in Welding: Discovering Causes, Effects, and Avoidance Methods
Porosity in welding is a consistent obstacle that can considerably affect the high quality and integrity of welds. As professionals in the welding industry are cognizant, comprehending the causes, impacts, and prevention methods connected to porosity is essential for attaining robust and reputable welds. By diving into the origin creates of porosity, analyzing its damaging impacts on weld quality, and discovering effective prevention methods, welders can boost their understanding and abilities to generate high-grade welds consistently. The detailed interplay of elements adding to porosity requires an extensive understanding and a proactive method to ensure effective welding outcomes.
Common Reasons For Porosity
Porosity in welding is mainly triggered by a mix of variables such as contamination, improper protecting, and poor gas protection throughout the welding procedure. Contamination, in the kind of dirt, oil, or corrosion on the welding surface, produces gas pockets when warmed, leading to porosity in the weld. Inappropriate protecting takes place when the shielding gas, typically made use of in procedures like MIG and TIG welding, is unable to fully protect the molten weld pool from responding with the bordering air, leading to gas entrapment and subsequent porosity. Furthermore, poor gas coverage, usually due to inaccurate circulation prices or nozzle positioning, can leave parts of the weld unsafe, permitting porosity to develop. These variables jointly add to the development of voids within the weld, compromising its stability and possibly triggering architectural concerns. Recognizing and addressing these common causes are essential actions in avoiding porosity and making certain the quality and stamina of bonded joints.
Results on Weld Quality
The presence of porosity in a weld can significantly compromise the total top quality and stability of the welded joint. Porosity within a weld creates gaps or dental caries that damage the structure, making it much more susceptible to cracking, deterioration, and mechanical failing. These spaces serve as stress concentrators, lowering the load-bearing capability of the weld and enhancing the likelihood of premature failing under used tension. Additionally, porosity can additionally serve as potential websites for hydrogen entrapment, more intensifying the degradation of the weld's mechanical homes.
Moreover, porosity can impede the efficiency of non-destructive testing (NDT) methods, making it challenging to spot other flaws or stoppages within the weld. This can result in substantial safety problems, especially in vital applications where the structural stability of the bonded you could check here components is critical.
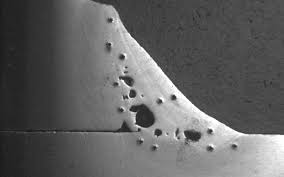
Prevention Techniques Review
Provided the damaging impact of porosity on weld high quality, effective prevention strategies are crucial to maintaining the architectural integrity of welded joints. Furthermore, selecting the appropriate welding parameters, such as voltage, current, and take a trip rate, can assist lessen the danger of porosity formation. By incorporating these avoidance strategies into welding methods, the occurrence of porosity can be substantially reduced, leading to stronger and a lot more trustworthy welded joints.
Importance of Correct Protecting
Proper protecting in welding plays a vital function in avoiding atmospheric contamination and making certain the honesty of welded joints. Shielding gases, such as argon, original site helium, or a combination of both, are frequently made use of to secure the weld pool from responding with aspects in the air like oxygen and nitrogen. When these responsive aspects come into contact with the warm weld pool, they can create porosity, causing weak welds with reduced mechanical properties.

Insufficient shielding can lead to various issues like porosity, spatter, and oxidation, jeopardizing the architectural stability of the bonded joint. Adhering to appropriate shielding methods is essential to create high-quality welds browse this site with very little issues and guarantee the long life and reliability of the welded elements.
Monitoring and Control Techniques
Just how can welders effectively check and regulate the welding process to guarantee ideal results and protect against issues like porosity? One key technique is via making use of sophisticated surveillance modern technologies. These can consist of real-time tracking systems that supply responses on parameters such as voltage, present, travel speed, and gas flow rates. By continually monitoring these variables, welders can identify variances from the excellent conditions and make immediate adjustments to stop porosity development.

In addition, executing proper training programs for welders is vital for keeping an eye on and managing the welding process efficiently. What is Porosity. Educating welders on the importance of maintaining consistent parameters, such as correct gas securing and take a trip speed, can help prevent porosity issues. Regular analyses and qualifications can additionally make sure that welders excel in tracking and controlling welding processes
Furthermore, using automated welding systems can improve tracking and control capabilities. These systems can specifically manage welding parameters, decreasing the likelihood of human mistake and making sure consistent weld quality. By incorporating sophisticated surveillance modern technologies, training programs, and automated systems, welders can successfully check and control the welding procedure to reduce porosity issues and achieve top notch welds.
Final Thought
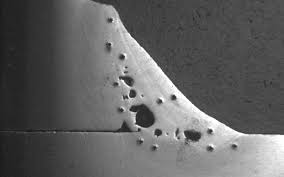
Comments on “What is Porosity in Welding: Usual Resources and Efficient Remedies”